Germany-based Cabka Group recycles post-industrial plastics into pallets and other material handling products. Cabka North America’ 400,000-square-foot plant in the St. Louis, Missouri area runs 24/7 to manufacture about 5,000 pallets per day.
But Cabka is challenged by labor shortages due to high turnover of temporary workers, which leads to expensive downtime. At Cabka North America’s facility, workers at eleven injection molding machines unload plastic pallets and manually trim and stack them for material handlers to transport to the warehouse using fork trucks or pallet jacks. The work is repetitive and physical, making it hard to retain workers, and the presence of fork trucks on the production floor leads to safety concerns.
However, a new, fully automated production line that will be replicated throughout the facility is helping minimize dependency on temporary workers while also improving product quality and worker safety.
A Mobile Industrial Robots MiR500 autonomous mobile robot is part of that fully automated production line. The production line also includes a Krauss Maffei six-axis robot to autonomously unload pallets from the injection molding machine, trim the pallets, and load the finished products directly onto the MiR500. The MiR500, which is equipped with a MiR pallet lift, transports the finished products out of the manufacturing floor to a separate staging area as soon as the job is complete.
In the staging area, the pallets can be checked for quality and wrapped. Fork trucks then transport the finished pallets to the warehouse and loading docks without having manufacturing workers present. This will allow Cabka to eliminate fork truck traffic in the production area, replacing them with safe, collaborative mobile robots.
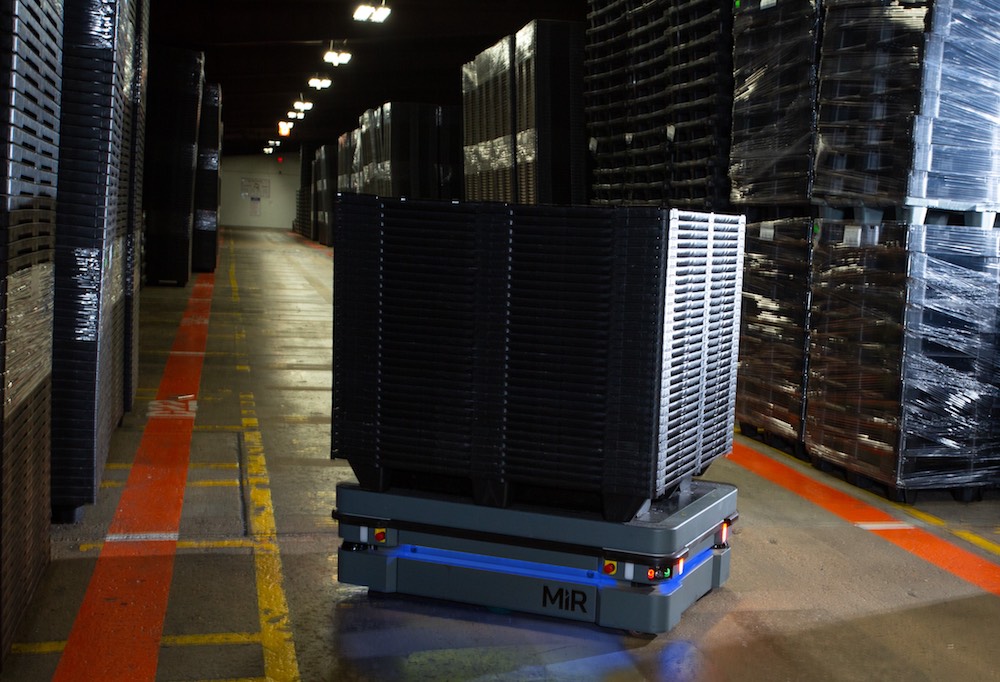
Cabka North America uses a MiR500 autonomous mobile robot to transport plastic pallets. | Credit: Mobile Industrial Robots
Pilot project leads to fully optimized production
The fully automated production line is intended to be the model for the eventual automation of all eleven production lines, with a fleet of MiR robots supporting them in a dynamic, highly efficient manufacturing floor. Each AMR can go where it’s needed when it’s needed to keep production flowing.
Cabka estimates the first MiR500 travels about three miles a day supporting one production line. With eleven lines planned for autonomous material transport with multiple MiR robots, workers and fork truck drivers will be relieved from many miles of manual material handling, allowing Cabka to redeploy those workers to higher-value tasks.
“With the MiR500, we are very happy with the payload,” said Cabka project technician Craig Bossler. “It’s handled everything that we can stack on top of it. We haven’t found out how high we can go yet. It’s very stable — it can make turns, go straight, and it can hit bumps, and it’s always very stable. The MiR definitely can handle all the imperfections in the floor.”

Production of MiR5000 autonomous mobile robots. The company says 40 percent of its sales has gone to the U.S. | Credit: Mobile Industrial Robots
Adding more MiR500 mobile robots
Cabka North America is looking at other ways to use the MiR robots, including prepping orders overnight in the warehouse so they will be ready at the dock for loading in the morning. Patrick Garin, president of Cabka North America, anticipates that other Cabka locations will be following the North American facility’s lead.
“We always have our corporate people come here – our corporate CEO and the other part of the team – and they will definitely be very interested in seeing our progress here,” he said.
Teradyne Inc. of North Reading, Mass., recently acquired Mobile Industrial Robots of Odense, Denmark. Three years ago, Teradyne also purchased another Danish automation company, collaborative robot maker Universal Robots.
The post MiR500 mobile robot helps Cabka automate pallet transport appeared first on The Robot Report.