The past few years have seen many organizations implement tech-driven changes at a rapid pace. As society becomes more digital, embracing technology and effectively managing new processes is key to the success of almost every business.
With rapid workplace transformation evident across industries, whether that’s moving to hybrid working or adopting new technologies, what can we expect from 2023? Here are five predictions for the coming year.
1. Turnkey solutions will make automation more accessible than ever
In recent years we have witnessed the development of many different types of sophisticated technologies. Advances in robotics, machine learning and other technologies have increased the pace of this change tenfold. While these promise to change or revolutionize the business world, all technology companies suffer from the same problem – they can’t be good at everything.
In the world of robotics, this is no different. Creating a robotic system requires hardware development, software development, application development, sensors, and interfaces to name a few. That’s why 2023 will be the year of turnkey solutions.
Original Equipment Manufacturers (OEMs) – companies creating new applications and products around existing technologies – will lie at the heart of this. They are able to drive innovation by combining technologies to deliver complete solutions for the most common applications, such as welding and palletizing. The result? Automation will become more sophisticated yet more straightforward to use than ever before.
Enabled Robotics, an OEM based in Denmark, is a great example of how this works. Since 2016 the company has been working to combine two types of cutting-edge technology by mounting collaborative robot arms (cobots) onto autonomous mobile robots (AMRs). This hybrid technology is now operating in industry, warehouse management and production and bringing robotics to service applications and hospital intralogistics.
Ultimately, these out-of-the-box solutions make it easier for companies to integrate crucial technologies and there is no limit to the imaginative ways companies will find to bring robots alongside humans in the world of work.
2. Manufacturers will turn towards modular production
Traditional industrial robots remain important in some parts of manufacturing, but we are seeing a trend towards deploying more flexible models of production. This is largely down to the fact that traditional industrial robots are typically large and fixed and entail complex deployment.
In contrast, cobots can perform a similar range of activities to traditional industrial robots but are smaller, lighter and much easier to deploy. They are designed to work alongside humans so pose less risk to safety and are better suited to environments that require flexibility and adaptability. On top of this, they are most cost-effective for businesses looking to deploy automation – a key consideration as we move into 2023.
The cobot industry is projected to grow to USD 2.2 billion by 2026 (The Collaborative Robot Market 2022 Report, Interact Analysis). As cobots continue to change the way work is done in applications such as packing, palletizing, welding and assembly, in 2023 we will see even larger companies turning to lightweight cobots to increase modularity in their production. Robot weight and versatility will be key specifications for those looking for new automation solutions and we will see more reconfigurable robotic work cells than ever before.
3. Higher payload and longer reach cobots will change the landscape for some applications
As more companies move towards cobot automation, many will still want to handle heavy payloads. The good news is that we have recently seen the introduction of several higher payload, longer reach cobots. In 2023 these will continue to transform parts of the manufacturing industry, improving the working lives of many employees.
This year, Universal Robots presented a new cobot, the UR20, which is built for higher payloads, faster speeds, and superior motion control all within a lightweight, small footprint system. The 20 kg payload capacity will transform industries such as palletizing while its 1750 mm reach is eagerly anticipated for use in welding. Manufacturers looking for that extra flexibility will find the robot light enough to be unbolted and relocated or attached to a heavy base with wheels. This will create new possibilities for applications and will drive innovation across the board. The UR20 will be delivered to customers in 2023.
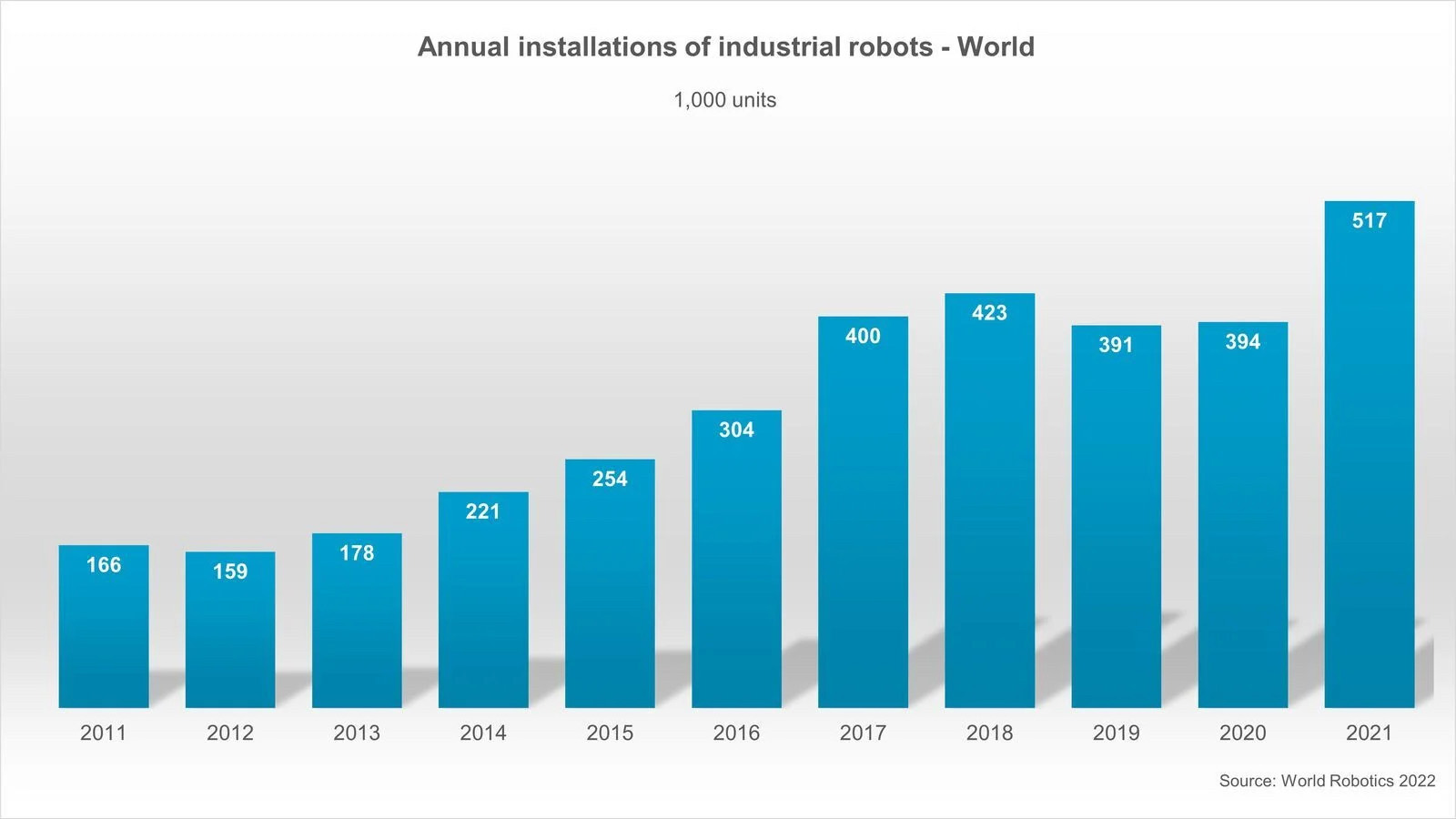
Annual installations of industrial robots worldwide. | Source: IFR
4. Despite global uncertainties, long-term increases in industrial robot installations will continue
The recent IFR World Robotics Report showed industrial robot installation reached an all-time high in 2021 increasing by 31% over the previous year. Overall, worldwide annual robot installations between 2015 and 2021 have more than doubled. Although growth in 2022 seems to be slower across the sector, this is largely down to global uncertainties triggered by the pandemic and scarcity of electronic components.
We expect the upward trend of cobot automation to resume in 2023. Why? Because businesses across the world are facing labor and skills shortages and, despite the day-to-day challenges facing industry right now, we are in the midst of transition towards industry 5.0 where working alongside robots will create more human-centric, sustainable and resilient businesses.
5. Customers will be found at the heart of product development
Although we talk extensively about robot collaboration in the workplace, human collaboration is what drives innovation.
Customers understand their own needs better than anyone else and, as the automation market has matured, are better placed than ever before to offer valuable input on their requirements. This means robotics companies will involve customers much more in product development. It is why Universal Robots has reorganized its product creation teams and is focusing heavily on understanding the problems customers are facing before designing solutions.
Co-development projects where robotics companies and customers work together in developing specific solutions are also bound to increase in 2023 and beyond. Ultimately these allow customers to directly influence the product they are buying, while at the same time delivering valuable feedback for the robotic companies – meaning they will be able to launch a product to the benefit of the whole market.
Now more than ever, businesses need to innovate constantly and remain adaptable in order to survive and expand. As we head into 2023, they will rely ever more on technology and innovation to break new ground with turnkey solutions at the heart – all of which make the year ahead an exciting time for automation.
About the Author
Anders Beck is the Vice President of Strategy and Innovation at Universal Robots, a leading developer of collaborative robot arms. Prior to his time at Universal Robots, he held a number of positions at the Teknologisk Institut in Denmark, including head of industrial robotics and automation.
The post 5 robotics predictions for 2023 appeared first on The Robot Report.