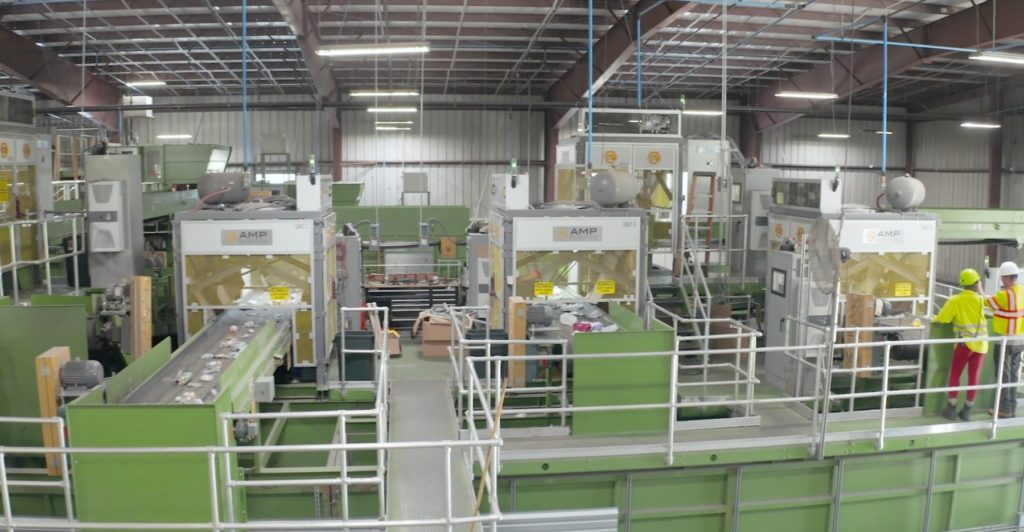
AMP robotics deployment at SSR in Florida. Source: Business Wire
DENVER — AMP Robotics Corp., a pioneer in artificial intelligence and robotics for the recycling industry, today announced the further expansion of AI guided robots for recycling municipal solid waste at Single Stream Recyclers LLC. This follows Single Stream Recyclers’ recent unveiling of its first installation of AMP systems at its state-of-the-art material recovery facility in Florida, the first of its kind in the state.
Single Stream Recyclers (SSR) currently operates six AMP Cortex single-robot systems at its 100,000 square-foot facility in Sarasota. The latest deployment will add another four AMP Cortex dual-robot systems (DRS), bringing the total deployment to 14 robots. The AMP Cortex DRS uses two high-speed precision robots that sort, pick, and place materials. The robots are installed on a number of different sorting lines throughout the facility and will process plastics, cartons, paper, cardboard, metals, and other materials.
“Robots are the future of the recycling industry,” said John Hansen co-owner of SSR. “Our investment with AMP is vital to our goal of creating the most efficient recycling operation possible, while producing the highest value commodities for resale.”
“AMP’s robots are highly reliable and can consistently pick 70-80 items a minute as needed, twice as fast as humanly possible and with greater accuracy,” added Eric Konik co-owner of SSR. “This will help us lower cost, remove contamination, increase the purity of our commodity bales, divert waste from the landfill, and increase overall recycling rates.”
AMP Neuron AI guides materials sorting
The AMP Cortex robots are guided by the AMP Neuron AI platform to perform tasks. AMP Neuron applies computer vision and machine learning to recognize different colors, textures, shapes, sizes, and patterns to identify material characteristics.
Exact down to what brand a package is, the system transforms millions of images into data, directing the robots to pick and place targeted material for recycling. The AI platform digitizes the material stream, capturing data on what goes in and out, so informed decisions can be made about operations.
“SSR has built a world-class facility that sets the bar for modern recycling. John, Eric and their team are at the forefront of their industry and we are grateful to be a part of their plans,” said Matanya Horowitz, CEO of AMP Robotics. “SSR represents the most comprehensive application of AI and robotics in the recycling industry, a major milestone not only for us, but for the advancement of the circular economy.”
The new systems will be installed this summer. Upon completion, AMP’s installation at SSR is believed to be the single largest application of AI guided robots for recycling in the United States and likely the world. In addition to Florida, AMP has installations at numerous facilities across the country including California, Colorado, Indiana, Minnesota, and Wisconsin; with many more planned. Earlier this spring, AMP expanded globally by partnering with Ryohshin Ltd. to bring robotic recycling to Japan.
About AMP Robotics
AMP Robotics is transforming the economics of recycling with AI-guided robots. The company’s high-performance industrial robotics system, AMP Cortex, precisely automates the identification, sorting, and processing of material streams to extract maximum value for businesses that recycle municipal solid waste, e-waste and construction and demolition.
The AMP Neuron AI platform operates AMP Cortex using advanced computer vision and machine learning to continuously train itself by processing millions of material images within an ever-expanding neural network that experientially adapts to changes in a facility’s material stream.
About Single Stream Recyclers
Single Stream Recyclers is a materials recovery facility in Sarasota, Fla. It processes, materials from all over the west coast of Florida. The facility sorts, bales and ships aluminum, cardboard, food and beverage cartons, glass, paper, plastics, metal and other recyclables from residential curbside and commercial recycling collection. SSR is heavily invested in technology to help create the best possible end products and reduce contamination as well as residue.